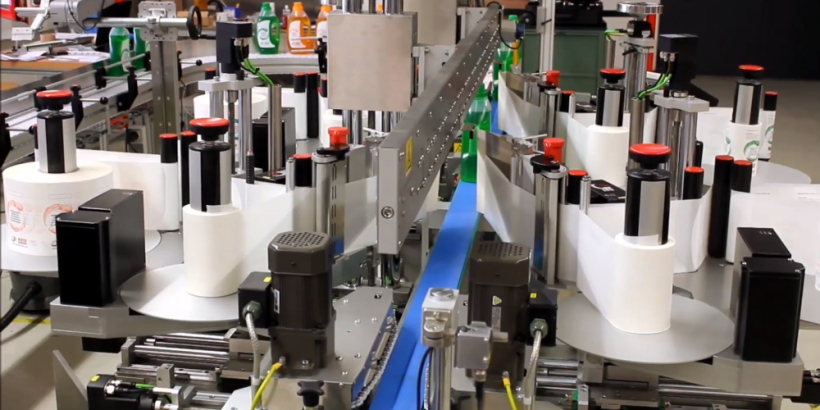
The right set-up seminars are offered about set-up time optimization. Here, specialists and executives from production, production planning, production control and logistics methods are to become acquainted with employee qualification and strategies for set-up time minimization.
De facto, however, the set-up time always depends on the design of the machine. Because when the machine must be manually adjusted at lot of different parts, this simply takes its time (apart from the error of the error) – because one of the most proficient employees does not use anything.
How would the “perfect” batch change for you? Probably now answer like most: “Fully automatic!” The machine automatically receives the information about which batch is next in the series and makes all the parameters fully automatic.
Fully automated batch exchange with BluhmWeber Group
We see that in the same way! Therefore, we have developed a system for product labelling that can fully adapt to the next product when the batch is changed: In the case of the Geset 314 ZDT, the respective labelling parameters such as position, inclination and distance of the label dispenser can be stored in the PLC. When the batch is changed, the specific parameters can be called up at the push of a button and the system can be fully automated with the help of numerous small actuators.
To simplify the initial setting-up of the labelling system, small digital displays are located on all actuators. Once the optimum position has been found, a push button is sufficient to store the setting. When the batch is changed, the PLC does not give “green light” for the labelling process until all labelling parameters have been set correctly. This creates additional production security and decimates committees.
A digital display for production safety is provided on each individual actuator of the Geset 314 ZDT.
The Geset 314 ZDT can do even more: ZDT stands for Zero Downtime and means that the label rolls can be refilled while the machine is running – without any production interruption.
In addition, the system can, for example, be provided with a colour sensor which allows the machine to emit different labels depending on the product colour.
Four Alpha HSM label dispensers are located in the system, enabling the labelling of products from several pages. Alternatively, two of the labellers can also be used for the additional application of marketing labels.
With a separate pre-roll, label rolls up to 500 mm in diameter can be processed. Depending on the product size, the serial labelling machine operates with clock rates of up to 250 products per minute. Since it consists of a base and head band depending on the application, even narrow, shaky packages can be safely guided during transport.
Geset labelling systems: More possibilities thanks to modular design
The Gebet series and special labelling division of BluhmWeber Group designs and manufactures tailor-made solutions that allow square, round and oval products on the front and back, as well as cylindrical and conical products to be labelled completely or partially. The dispensing technique is used either for pre-printed labels or in combination with other technologies – inkjet, laser or thermal transfer printing – to write variable data to the label before the actual labelling process. The numerous function modules are standardized and can be assembled and extended in all variants.