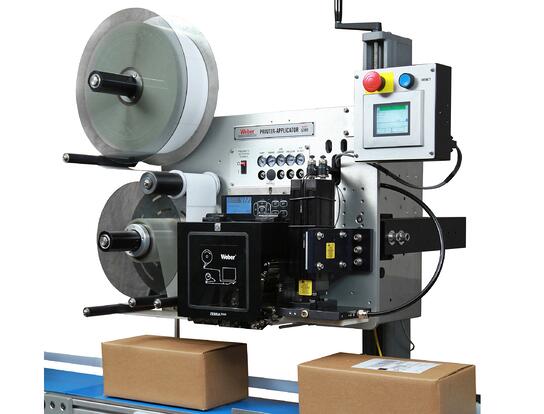
In the world of labeling, every detail counts. The way you label your products can impact everything from your operational costs to customer satisfaction. While manual labeling might suffice for smaller enterprises, the moment your business starts to expand, label automation becomes not just a smart move, but a strategic imperative.
In this comprehensive guide, we’ll go beyond the initial four benefits and explore the full spectrum of reasons why you need label automation from Weber Packaging Solutions.
Labour Savings with Label Automation
Labour costs are a significant overhead for any business. By investing in label automation upfront, you can free your employees to focus on more value-added tasks. What’s more, label automation systems are built to last, ensuring long-term savings in labour expenses.
Quality label automation, meticulously tailored to your specific needs, can serve you for years, allowing your business to expand and meet customer demands without the need to hire additional staff for labeling.
Consistent Label Placement
Manual label application, especially at high throughputs, often results in inconsistent label placement. When a human operator peels a label off a liner and applies it to a product, perfection isn’t guaranteed. Labels can end up crooked, wrinkled, or misplaced, leading to issues like poor shelf appeal, barcode damage, or label detachment.
Label automation ensures precise label placement, regardless of the throughput rate. This consistency maintains the visual appeal of your products and minimizes costly labeling errors.
Keeping Up with Demand
As your business grows, so does the demand for your products. With manual labeling, a surge in demand might necessitate hiring more labor or reassigning workers from other critical projects. This not only strains your resources but can also affect overall productivity.
Label automation can seamlessly scale up with increasing demand, eliminating the need for frequent workforce adjustments. You can meet customer needs efficiently without compromising other aspects of your operation.
Reduced Label Errors
Label automation introduces verification options to ensure accuracy. Scanners and imagers double-check that the right label is applied to the correct product, making certain that barcodes and text are legible. In contrast, manual labeling is inherently more susceptible to human error, which can result in costly mistakes.
Beyond these initial four reasons, let’s explore the two primary types of label automation offered by Weber Packaging Solutions:
Primary Label Automation: This involves applying fully pre-printed labels directly to products of various sizes and shapes. Whether you’re in the food industry, dealing with jelly jars, bakery clamshell containers, or wine bottles, or working with health and beauty products like shampoos and lotions, primary label automation offers substantial benefits.
Print-Apply Label Automation: This process adds variable printing to labels before applying them to products. The most common application is labeling corrugated cartons with variably printed shipping labels. However, it extends to printing ingredients and nutritional facts on food product labels, adding warnings to chemical containers, or including serial numbers on labels for appliances and circuit boards.
In both primary and print-apply applications, manual labeling remains an option. However, envision the time, money, and productivity gains achievable through investing in an accurate label automation system. The advantages are far-reaching, from increased efficiency to enhanced quality control.
To embark on your label automation journey or to upgrade your existing labeling systems, we encourage you to speak with a Weber Label Expert. They can help you explore tailored solutions that align with your specific needs, optimizing your labeling process and contributing to the overall success of your business. Don’t let manual labeling hold you back when label automation can propel you forward.